
230 V | 400 V
GMK2
granulator
The plastic granulator shreds plastic into small flakes.
Applied by hundreds of users around the world in a wide range of applications, the plasticpreneur granulator is the perfect choice to prepare plastic waste for injection moulding or extrusion processing.
List price
230 V: 8,590 € (excl. VAT)
400 V: 7,890 € (excl. VAT)
Included: tools & safety gear set

EXPLORE
experience and showcase the recycling process hands-on
CREATE
fast and cost effective way to create prototypes
MANUFACTURE
small batch to series production of tens of thousands of units

GMK2
machine
features
Developed in cooperation with one of the leading manufacturers of plastic granulators in Central Europe, with decades of expertise.
Improved ‘pull–in’ action of the rotor for bulky parts and sprues.
Replaceable and regrindable cutting blades.
Custom and EU-made, high quality cutting chamber box.
1
2
3
4
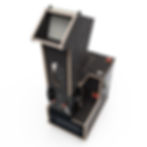
230V
GMK2 - granulator
standout qualities
CERTIFIED
CE/UKCA-certified & third party approved
EFFICIENT
energy efficient & optimised performance
RELIABLE
industrial components & maintenance friendly
WORKFLOW
pre-assembled & ready to use within minutes

230V | 400V
GMK2 - granulator
technical
features
GMK2- Granulator 230 V:
Electric: 200-240 V, 50-60 Hz
Power consumption: 2,200 W, 10 A
GMK2- Granulator 400 V:
Electric: 380-415 V, 50-60 Hz,
Power consumption: 2,200 W, 5.5 A
Plug Types
Type F (EU), Type G (GBR), Type B – Adapter (USA, CAN, JPN)
Dimensions: 47 x 77 x 135 cm (L x W x H)
Weight: 140 kg
Shipping dimensions: 80 x 60 x 105 cm (L x W x H)
Shipping weight: 170 kg (including accessories kit)
Packaging: half pallet with wooden/cardboard boxCE, UKCA
DIN EN ISO 14118, DIN EN ISO 14119, DIN EN 60204-1, DIN EN ISO 12100, DIN EN ISO 13849-1, DIN EN ISO 13849-2, DIN EN ISO 13850, DIN EN ISO 13857
Setup: stand alone, movable with casters
Hopper opening: 210 x 180 mm
max. wall thickness of plastic parts to be shredded: 10 mm
Rotor diameter: 130 mm
Rotor knives: 9 pcs
Stator knives: 2 pcs
Sieve opening/flake size: 5 mm (default size for delivery)
Additional available sieve/flake sizes: 6 and 8 mm
Output 5mm: 18 kg/h*
Output 6mm: 30 kg/h*
Output 8mm: 53 kg/h*
*with standard HDPE bottle caps
Noise no-load operation: 73 dB
Noise granulating polyolefins: < 75 dB
Noise granulating Acryl or PC: < 80 dB
Customs tariff number: HS84778091
GMK2 - granulator
distinctive features

granulating chamber
custom, EU-made, hardened components within the cutting chamber reduce wear from abrasive materials.

stand-alone & moveable
with casters. Ideal for an efficient workflow, safe process, and easy transport.

quick release
levers
for a safe and fast workflow, transportation and maintenance.

flexible
curtain
serves as splash protection and safety feature.

viewing
windows
3 viewing windows to watch the grinding process.

compact
design
enables universal applications on small spaces.
more distinctive features
< 5mm with low dust content due to optimised rotor design.
Within the cutting chamber reduces wear from abrasive materials.
Guarantee long-term use and durability.
For long lasting and sustainable use.
Lightweight, rigid and self-supporting structure with a unique design.
For safe shipping and transport worldwide. Heavy duty velcro fastener strips hold the GMK2 in place and allow a smooth and reusable packing and unpacking process.
the workflow
1
You are ready to create your first products within minutes. All of the necessary tools and safety gear for getting your machine operational are included.
2
The Machine is set up stand-alone in a well ventilated and dry room. It is easily movable with casters from one place to the other.
3
For an ideal workflow we suggest a well ventilated room, a space of 3-4 m².
getting started
the granulating process
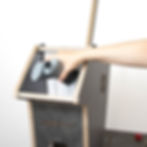
Washed and sorted plastic is fed into the hopper and enters the cutting box. Blades on a motor driven rotor, grind the plastic into small flakes. Through watching windows this process can be observed.
The grinding process takes place between the rotating rotor blades and the stationary stator blades. The cutting gap size and the cutting geometry of the rotor and stator blades can be adjusted.
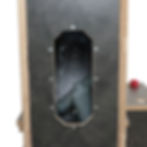

After passing through an exchangeable sieve, the flakes are collected in a box and are ready to be processed further in our injection moulding machine or extruder. The sieve size determines the flake size.
Larger plastic objects need to be pre cut to fit into the hopper. The hopper-pusher is used to feed thin-walled or round shaped plastic towards the blades for an efficient and safe cutting process.

Recommended for rigid polyolefins
Compatible with: flexible material such as TPU
Ability to test other materials such as biodegradable etc.
We assume no liability if materials other than those recommended are used. For other materials (e.g. biodegradable plastics) if applicable we can provide information as well as material tests.
Not recommended for use: stretch film, foamed materials
Never to use: wood, metall, electronics, etc.
Plastic may be pre-cut to fit into the hopper. E.g. with tin snips, saw, etc.
An accessory kit consisting of all needed parts to ensure safe and easy set up, as well as for maintenance are included.
This includes:-
Tool & safety gear set including
-
Ring spanner, flat screwdriver, tin snips
-
Gloves, safety glasses, ear protection
-
-
To safely operate the machine: gloves, safety glasses, and optional ear protection are needed. Depending on the input material the dB level varies. Therefore, we recommend using ear protection, especially if working for a longer period of time.
We ship worldwide.
The machine comes in tailor made packaging on a half pallet, or if ordered in a set together with other machines, via freight-forwarding on a pallet.